After serving in the U.S. Army Corps of Engineers and the Ordnance Corps during World War II, Lee Hunter returns home to St. Louis to open Hunter Engineering Company on Hunter Avenue in Ladue, Missouri.
Our History
Hunter Engineering, founded by Lee Hunter, has a rich history built on innovation and excellence.
Hunter History
Lee Hunter & Hunter Engineering
Hunter Engineering Company owes its beginnings to a discharged automobile battery. Lee Hunter Jr., a 23-year-old St. Louis architecture student, found himself frequently confronted with car battery failure in his Packard convertible.
When experts said it couldn't be done, Lee Hunter invented a way to quick charge automobile batteries. He then went on to build a highly successful company to manufacture and sell his other inventions that would soon after revolutionize the automotive service industry.
Today, Hunter Engineering Company designs, manufactures and sells a wide range of auto service equipment for a global market. Hunter products include PC- and Windows®-based wheel alignment systems, computerized wheel balancers, versatile tire changers, on- and off-car brake lathes, feature-packed vehicle lifts and money-saving inspection equipment.
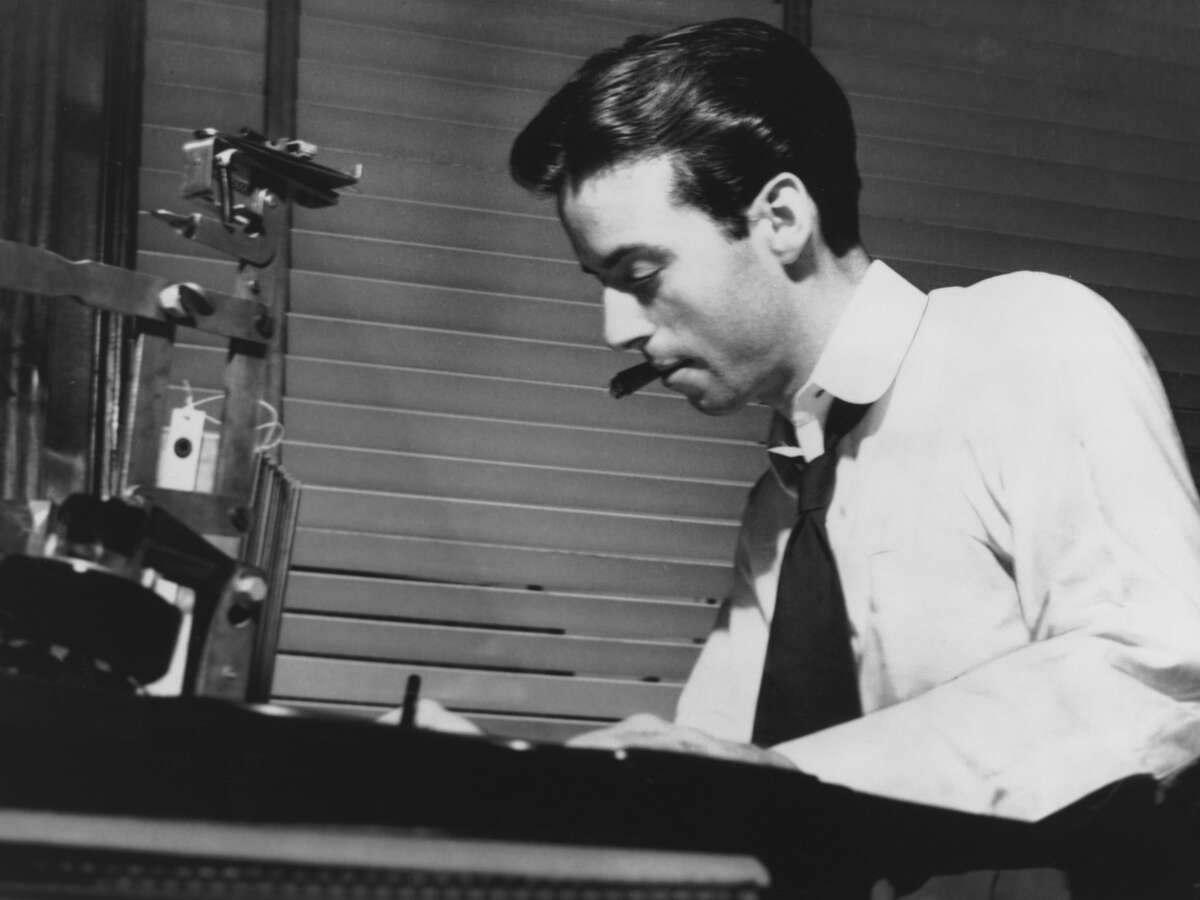
1930s
Kwikurent
1936
Kwikurent, the world’s first rapid battery charger, reduced charging time from 24 hours or more down to less than an hour, eliminating the need to remove the battery from the car. It was a revolution in the industry that sold as fast as the company could build them.
Rocket Special
1938
Set out to shrink the design into a more compact form, Lee Hunter introduced the Rocket Special that included a dual-charge test meter that analyzed voltage gravity in 10 seconds and an 100-ampere output for maximum charging speed. It also operated on a more widely accessible 110-volt circuit.
1940s
Return home
1946
Tune-In wheel balancer
1946
The Tune-In wheel balancer, Hunter Engineering's debut product, is a revolutionary on-the-car balancer and Lee Hunter invention.
First brochure
1949
Form 8-T, produced in June of 1949, is the company’s first product brochure.
1950s
Sales & service team
1950
Lee Hunter began assembling what would later become the largest dedicated sales and service team in the tire service equipment industry.
Sales meetings
1952
Sales Representatives become a driving force behind Hunter Engineering’s growth. Sales meetings and group photos become a Hunter tradition.
GM approval
1953
General Motors opens a plant in St. Louis to build the Corvette. This custom installation ensures every Corvette wheel is balanced using Hunter equipment.
The Vic Mathewson Distributor
1950's
The Vic Mathewson Company Limited, Canada's largest automotive distributor, was Hunter's Canadian distributor and representative in the 1950's.
Lite-A-Line
1955
Hunter Engineering develops the Lite-A-Line wheel alignment system. It soon becomes the industry standard.
More configurations
1955
Hunter develops multiple configurations of the Lite-A-Line system.
1960s
Hunter staff
1960
Hunter Engineering has a small but growing staff. Pictured here, the Engineering, Advertising, and Inspection departments all work side-by-side.
"Happy Hunter"
1962
“Happy Hunter” was a staple in early Hunter advertising and training films.
Sales conventions
1962
The 1962 Annual Sales Convention was held in St. Louis.
Relocation & expansion
1964
Hunter outgrows its original facility and relocates to a 23-acre campus next to St. Louis Airport. The location features new offices and manufacturing complex more than triple the size of the original.
Ford partnership
1964
After rigorous testing, Ford Motor Company names Hunter its sole supplier of alignment and balancing equipment.
Heavy-duty alignment
1967
Hunter alignment systems expand to cover heavy-duty applications.
Trade shows
1967
Hunter continues to expand its presence at top industry trade shows in the United States and Canada.
Compute-A-Line
1969
The F-60 and F-70 Compute-A-Line systems were the industry's first dynamic wheel alignment systems. Adjustments could be made without moving the vehicle and while the wheels are turning.
1970s
Research & Training Center
1973
The Hunter Research & Training Center opens adjacent to the company headquarters.
Rapid Series balancers
1974
Hunter introduces the Rapid Series balancers, signaling the dawn of dynamic, off-car wheel balancing.
S4 Electron-A-Line
1974
The S4 Electron-A-Line was the first electronic-metered system that featured electronic camber, caster and toe measurements, and electronic wheel runout compensation.
Ride Perfection Center
1974
Hunter’s Ride Perfection Center in operation. The RPC relieved portions of the sidewall to reduce radial force variation.
Advanced alignment systems
1975
The original Lite-A-Line system (left) is joined by the S5 Electron-A-Line, Tune-A-Line II, and Autron-A-Line series of aligners. Advanced Wheel Alignment systems become Hunter’s core focus.
Durant, MS manufacturing
1976
Hunter opens a manufacturing facility in Durant, Mississippi, to accommodate demand for a growing product line. The area bordered in red shows the layout of the original 1976 facility.
S7 Electron-A-Line
1979
Hunter’s S7 Electron-A-Line introduces the thrust-line principle to wheel alignment which becomes the foundation of modern four-wheel alignment technology.
1980s
Hunter Automotive Limited
1980
Hunter incorporates its Canadian operations into Hunter Automotive Limited to handle product distribution throughout Canada.
Hunter Canada moves
1980
Hunter Canada moves to Markham, ON, doubling warehouse space to 12,000 SF and adding a parts room, classroom, offices and training bay.
Leadership change
1981
Stephen F. Brauer appointed President, marking the first leadership change since Lee Hunter founded Hunter Engineering. Brauer guides the company into a period of rapid growth with the integration of new computer technology.
A111 wheel aligner
1982
The first CRT display wheel aligner allowed technicians to see measurements on screen.
Sales & service meetings
1983
A growing field organization attends the 1983 National Sales and Service Meeting from September 21-24.
Raymond, MS manufacturing
1984
Construction begins on the new production facility in Raymond, MS, which opens the following year.
C111 wheel aligner
1985
The C111 starts its production run in January 1985 with the aid of a little “Old Forester” — the traditional blessing of a new product.
Hunter Canada moves to Richmond Hill, ON
1986
Hunter Canada moves again to Richmond Hill ON, increasing space to 15,400 SF, upgrading Power Bay and increasing warehouse and office space.
Strong partnerships
1986
Lee Hunter meets with Hunter’s Japanese distributor, Iyasaka Ltd., maintaining a strong partnership that began almost a quarter-century before, in the 1960s.
Wheel-mounted sensors
1987
The first wheel-mounted sensors that process measurements on the sensor itself (a predecessor of the future DSP series sensors) provides fast, accurate alignment readings.
RL lift rack
1988
The RL rack featured fully floating rear slipplates, air line kit, retractable work steps and built-in turnplate pockets.
Brake testing
1989
The B400 computerized brake tester measures brake performance with a 4-minute drive-through process.
1990s
Hunter Service Center
1991
The Hunter Super Service Center opens and serves as the main distribution center for replacement parts in the U.S.
Windows® partnership
1992
WinAlign® recognized as the first Windows®-based vehicle alignment system.
Automotive Hall of Fame
1992
Lee Hunter inducted into the Automotive Hall of Fame where he shares the spotlight with industry giants such as Henry Ford, Louis Chevrolet, Walter P. Chrysler and Soichiro Honda.
DSP9000 balancer
1993
The DSP9000 balancer is the first to use digital signal processing for unparalleled accuracy.
Truck Safety Center
1993
The Truck Safety Center expands research, product development and technician training for heavy-duty vehicles.
P211 alignment system
1993
The P211 is the first PC-based alignment machine, featuring Windows®-based WinAlign® software and DSP200 series sensors.
TC325 tire changer
1995
The TC325 features Hunter exclusive “tulip” clamping system, ergonomic design and three-point articulated mounting arm – features found on many Hunter tire changers to this day.
DSP200 series sensors
1995
The DSP200 and DSP250 series wheel alignment sensors become the industry standard, featuring infrared beams that link together to produce accurate alignment measurements.
BL500 brake lathe
1996
The BL500 is the first brake lathe to offer Digi-Cal technology which instantly measures drum or rotor dimensions to help technicians determine total indicated runout.
411 series alignment system
1997
The 411 Series Alignment System features industry-leading technology including the most advanced personal computing hardware.
GSP9700 wheel balancer
1998
The GSP9700 offers a simulated road test to diagnose and solve non-balance related wheel vibration issues, transforming this wheel balancer into a wheel diagnostic center.
DSP400 camera sensors
1998
DSP400 digital imaging sensors feature durable, easy-to-handle reflective targets. Four cameras in the aligner tower measure the position and orientation of each wheel-mounted target which instantly provide initial wheel alignment measurements.
1998
The TC3250 features a tilted ergonomic design. With the addition of the “Plus” device, this versatile machine becomes Hunter’s most popular EMT approved tire changer.
RM lift rack
1999
The innovative design of the RM lift rack allows easy service access through its split front design.
2000s
Four-Post lift racks
2001
L421 (14,000 lb.) and L424 (16,000 lb.) alignment racks are introduced featuring longer slipplates than previous generations.
RX9 scissor lift rack
2001
The RX9 alignment rack offers several popular features including an open front and rear design for easy service access, extra-wide 24" runways, integrated air line kits, and the option to mount the rack flush with the floor.
GSP9712 wheel balancer
2002
Hunter Chairman, Steve Brauer, leads the traditional christening for the first GSP9712. The revolutionary wheel balancing system features industry firsts such as StraightTrak® which measures and corrects tire pull issues.
Hunter Canada moves to Newmarket, ON
2002
Hunter Canada moves to Newmark, ON.
Hunter Deutschland GmbH
2002
Hunter Deutschland GmbH opens. The office and training facility near Munich offers German car manufacturers the same engineering support available to U.S. manufacturers.
811 alignment system
2003
The 811 aligner, combined with DSP600 digital imaging sensors and WinAlign® 7.0, features increased productivity, profitability and value. This system leads the industry for five years.
DSP500T sensors
2004
Designed specifically for heavy-duty applications, the DSP500T series alignment sensors offer measurement accuracy and repeatability never before seen in the heavy-duty industry.
OEM approvals
2004
Hunter Engineering’s state-of-the-art digital imaging alignment systems gain approval by BMW, Daimler Chrysler and the Volkswagen Audi Group (VAG). Hunter remains the only alignment supplier with all three German automaker approvals.
SmartWeight®
2005
Revolutionary SmartWeight® Balancing Technology is introduced. This patented balancing method improves wheel balancing results while minimizing the amount of corrective weight applied by the operator.
TCX500 series tire changers
2005
The TCX500 family of tire changers are introduced. This group of table-top tire changer offers coverage for passenger car to medium duty vehicles. This line of changers will go on to become an industry staple and Hunter best-selling series.
GSP9200 balancer
2006
The GSP9200 balancer is introduced. Though intended as a compact model, it is packed with advanced features including SmartWeight® laser line weight placement, auto double Dataset® arms, Spindle-Lok®, rim scan and Quick-Thread®.
Durant, MS 30 years
2006
Durant, Mississippi, reaches a milestone and celebrates 30 years of fabricating and assembling Hunter lift racks.
GSP9700 improvements
2007
The third generation GSP9700 improves on Hunter’s most popular model by featuring improvements such as a Linux operating system, color LCD monitor, thumb drive data port and the ability to have a custom logo on the welcome screen.
WinAlign® 10.0
2007
Using the new WinAlign® 10.0 software, the HawkEye® high definition digital imaging wheel alignment system is introduced with smaller, lighter sensors designed for speed and efficiency.
Auto34 tire changer
2008
The Auto34 introduces a new level of control to tire changing with a simple control panel. Technicians are able to perform all operations without the traditional lever.
SmartWeight® balancer
2009
Hunter formally introduces the SmartWeight® balancer — a highly productive balancer designed for every shop. Fully-integrated with SmartWeight Balancing Technology® it also features many powerful options including a wheel lift, AutoClamp, a top dead center laser system, and a printer.
Four-Post improvements
2009
The L441 and L444 four-post lift racks provide 18,000 lbs of lifting capacity and the option of an open- or closed-front designs.
2010s
WinAlign® improvements
2010
WinAlign® 11.1 features improvements such as new CodeLink® printouts and support for the DSP700 sensors. The TouchRemote® app for the iPhone® adds a new dynamic to WinAlign®.
HawkEye Elite®
2011
HE421 HawkEye Elite® with TD targets introduced. True three-dimensional targets that eliminate metal to metal contact as well as the need to carefully center the target. This system proves faster, lighter, more durable and changes the way shops align vehicles.
Hunter China
2011
Hunter China opens a wholly owned subsidiary office in Beijing China. The Chinese market is in a period of rapid growth and expansion.
Quick Check®
2012
Hunters Quick Check® system offers fast and accurate alignment checks right from the service drive. This system becomes one of Hunter Engineering's bestsellers and in record time.
RX lift rack improvements
2012
The RX series of racks expands with the introduction of the RX16. The surface mount version sits at only 9” when lowered but with the innovative Power-Up feature, the rack changes its lifting point allowing it to maximize capacity.
DSP700T sensors
2013
DSP700T sensors are introduced to the Heavy-Duty market. These sensors allow for all three axles to be measured at the same time. Designed to mimic the accuracy and convince of the passenger car system, the Heavy-Duty world now has a lightweight, fast and accurate equivalent.
Raymond, MS expansion
2014
Hunter’s Raymond, MS manufacturing plant expansion adds 66,000 square feet to include a state-of-the-art electronics facility to produce sophisticated electronic assemblies for many Hunter products.
Revolution™ tire changer
2014
The Revolution™ is the industry's first reliable, computerized and automatic tire changer. The Revolution™ uses an automated process for all tire and wheel combinations which turns all technicians into experts. It has the distinction of being the world's first UL Listed tire changer and was completely designed and built in the USA.
Hunter Canada expands
2014
Experiencing tremendous growth in the Canadian market, Hunter Canada moves to a new facility. The building provides conference rooms and a complete Power Bay, modeled after the original at St. Louis headquarters.
Quick Tread®
2015
Tire health took center stage in 2015 with the introduction of Quick Tread®. The system scans all four tire in seconds and creates a 3-D model. The imaging from the model provides a true tire health report for customers.
SEMA Show
2016
Hunter Engineering became the largest non-OE exhibitor at the SEMA Show with a 7,000 square foot booth staffed by over 100 HQ employees and members of Hunter's field organization.
Road Force® Elite
2017
The Road Force® Elite, uses patented Hunter vision technology to automatically determine wheel dimensions and wheel runout measurements. GM announces the Road Force® Elite as essential equipment for use in service facilities in the U.S.
AutoComp Elite®
2017
The AutoComp Elite® introduced patented Automatic Compensation technology and an intuitive touchscreen interface. It also gained OE approval at an unprecedented rate.
Autonomous features
2018
The Revolution™ WalkAway™ allows for 80-second autonomous operation during the bead breaking and demounting process, and offers time saving of 25% or more when paired with wheel balancing.
Unmanned inspection
2019
Quick Check Drive® provides unmanned alignment audit results with no stopping or labor required. Additional cameras can capture 40+ images per vehicle, protecting shops against mistaken damage claims.
2020s
BL Series bench lathe
2020
The BL Series bench lathe brings speed, precision and versatility to brake service, plus Anti-Chatter Technology to eliminate virtually all vibration buildup.
HunterNet® 2 portal
2020
The first of its kind in the industry, HunterNet® 2 online portal allows customers to track ROI, set goals, order consumables, and view and manage all of their Hunter equipment in real time.
75 Years
2021
Hunter Engineering celebrates 75 years of innovative, standard-setting products, built in the USA from a solid foundation of ingenuity, craftsmanship and service excellence.
ADAS calibration tools
2021
Hunter enters the booming ADAS market with the ADASLink® full-diagnostic scan tool, providing techs with quick access to step-by-step calibration procedures for more than 25 million vehicles.
Heavy-Duty Four-Post
2021
High capacity is the chief characteristic of the Heavy-Duty Four-Post alignment lift for commercial vehicles, offering 35,000-lbs. capacity and 300-in. wheelbase capabilities for safe and quick service.
Quick Check® Commercial
2021
Quick Check® Commercial makes Hunter the first global provider to introduce a touchless commercial inspection solution for measuring camber, total toe, tandem axle scrub and tire tread on all axles, on all trucks.
Maverick® Tire Changer
2022
The Maverick® premium center-clamp tire changer brings precision and power to a technician-driven machine, combining low-speed automatic functionality with faster, fully variable controls.
Mississippi Distribution Center
2022
Hunter opens a new 106,000-square-foot, 37-bay distribution center in Madison, MS, allowing production facilities more room and providing more efficient shipping to customers from a single location.
Hunter Deutschland Facility
2023
The 1150 spm facility in Puchheim, Germany contains a well-equipped, high-rack warehouse with European logistical support hub, training facility for service and user training, and lab area to support R&D cooperation with European OEs.
Ultimate ADAS™
2023
Ultimate ADAS ™ lives up to its name via innovative gimbal-mounted lasers that replace error-prone manual layouts and cut target placement time by 70 percent for some procedures.
HawkEye® XL
2023
The Hawkeye ® XL aligner's precise high-definition cameras provide extra-long-range sight, capturing measurements in four minutes and displaying live alignment readings for up to three axles at once.
Hunter Canada remodel
2025
Hunter Engineering Canada completes a remodel and redesign of its distribution center in Aurora, ON to significantly increase inventory capacity.